It’s probably safe to say that roof repair is about as enjoyable as a zookeeper being tasked with feeding the animals.
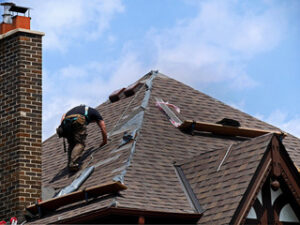
It’s a necessary chore nobody wants to do, but it must be done to protect everything inside your home. Every day you put off roof repairs is another day that moisture, toxins, and other damage can trickle down into your living spaces.
The majority of roofing repair jobs that you can do yourself involve shingles and other surface issues. Replacing a damaged shingle or two and repairing cracks or other minor damage can be accomplished quickly and inexpensively. However, if the roof has sustained major damage or you find that there is a leak, it may be best to call in professionals for an inspection and estimate for replacement and repair.
The shingles of a roof are a primary defense against water and other debris that might cause serious problems down the road. The most obvious sign of shingle damage is a patch that appears darker or wet than the surrounding area. This indicates that moisture has collected under the shingle, possibly leading to a leak and potential water stains on walls or ceilings inside the house.
Another way to detect shingle damage is to inspect the roof for a missing shingle or two. Loose shingles can often be re-secured by nailing through the top of the shingle tabs. If you find that a shingle has been dislodged completely, the entire shingle strip should be replaced.
When you do replace a shingle, make sure that the replacement is of a similar style and color to the rest of the shingles on the roof for a cohesive appearance. If you’re unable to locate a replacement that matches, it is sometimes possible to camouflage the new shingle by applying a layer of sealant beneath it.
If a shingle has been subjected to significant wind pressures, it may be creased or flipped and have lost the adhesive strip that holds it in place. The most common modes of shingle failure due to exposure to extreme wind include creasing (where the shingle tab is bent up and down repeatedly, creating a crease or fold along the edge of the shingle above); flipping, where the shingle tab is folded back over itself; tearing, where the shingle is ripped off; punctures from hail or other impact; and nail pull through.
To replace a shingle, first gather the necessary tools for the job, including a hammer, a flat pry bar, a utility knife and some 1-1/4-in. roofing nails. Slide the pry bar underneath the shingle directly above the damaged section and lift slowly to break the sealer strip connection and expose the first row of nails. Next, slide the pry bar under and gently lift the shingle to remove it and expose the second row of nails.
Leaking Pipes
The famous author John Bunyan once said that “one leak will sink a ship.” He wasn’t speaking literally, of course, but his logic holds true: a small problem like a leaking pipe can quickly escalate into a huge one. This is especially true if you neglect it long enough. The water can damage drywall, stain wood and carpeting, or even create a major health hazard with mold growth. It can also cause the water bill to skyrocket.
The simplest way to fix a leaking pipe is to simply wrap some waterproof tape around it. This will provide a temporary solution and can prevent further damage until you can call a plumber. It is important to make sure the area surrounding the pipe is completely dry before wrapping it. You can use duct or Teflon tape for this, depending on the type of pipe.
A more permanent option is to use a pipe repair clamp. These can be purchased at most hardware stores and require minimal mechanical skill. It’s important to follow the package instructions, however, as different products work differently. For instance, some require you to center the rubber sleeve over the damaged portion of the pipe, while others simply need you to bolt it into place.
Another potential problem with leaking pipes is that the water can become corrosive and discolor your home’s interior walls, flooring or ceilings. The stains can be difficult to spot because the water may travel along the joists or framing members before reaching the surface. This is why it’s so important to find the source of the leak and to address it promptly.
Leaking pipes can be very expensive to repair, but they’re also expensive to ignore. If you don’t address them, they can cause a wide range of problems, from poor water quality to warped and stained walls to invasive black mold. A plumber can assess the situation and recommend a repair plan that will stop the leaks and avoid expensive water-related damage to your home. In the end, fixing a leaking pipe can save you thousands of dollars in repairs and prevent costly water damage to other parts of your home.
Damaged Flashings
Flashings are the thin pieces of metal that line roof valleys and prevent leaks around chimneys, vents, skylights, dormers, and other roof penetrations. Although they are made from a wide variety of strong and durable materials, they are prone to damage from extreme weather conditions, age, and poor installation. Damage to flashings can leave the interior of a home exposed to water damage and may require cleaning, resealing, or replacement. Fortunately, it’s relatively easy for an experienced commercial roofer to repair or replace damaged flashings.
One of the most common signs that flashings need attention is corrosion. Corrosion is caused by exposure to extreme temperatures, which causes the metal to expand and contract. This constant bending can eventually weaken the flashing and cause it to crack or break. In some cases, the corrosion can spread to shingles or other roof material, which can create holes that will allow water to seep through and damage the interior of a home.
Another sign of damaged flashings is rust. Although rust is not as serious as corrosion, it can still degrade the flashing and leave it vulnerable to leaks. Luckily, rust is often easy to remove using a wire brush or heavy-duty sandpaper. Once the rusted area is clean, it’s easy to fill the hole with roofing cement or other appropriate patching materials.
Other common signs of flashing damage include dents or bends in the metal. These may seem minor, but they can compromise the galvanized coating of steel flashings and make them more susceptible to leaks. Additionally, high winds can sometimes cause flashing to become loose and fall off of the roof.
If you notice any of these problems, it’s best to call a professional commercial roofer right away. They’ll be able to inspect the roof and determine whether or not the flashing is the source of the problem. If it is, they can replace the flashing and seal any open areas that may be leaking water into the home. They’ll also be able to check for any other areas of the roof that are causing problems and fix them as necessary.
Mold
Mold is a type of fungus that is commonly found in indoor spaces. The spores of these fungi can be breathed in and cause health problems for certain people, especially infants and the elderly. Molds feed on dead organic matter and emit toxins that can irritate the eyes, nose, throat, and lungs when inhaled. They are also capable of causing damage to the surface materials on which they grow. Mold growth is a problem for homeowners because it can turn prized possessions into musty relics fit only for the garbage.
Molds are common in indoor spaces where there is moisture, such as in places with leaks in roofs, walls, pipes, and plants or where water has come in contact with building materials like wood or paper products. They are also common in areas with a lot of sunlight, such as basements and attics. Wet cellulose materials like wallpaper, insulation, drywall, and carpet provide ideal growing conditions for molds. Cladosporium, Penicillium, and Aspergillus are some of the most common indoor molds.
Toxic molds, including Stachybotrys Chartarum (also known as black mold), produce mycotoxins which are poisonous chemicals that have been shown to cause a variety of health issues. These opportunistic pathogens most commonly attack people with a suppressed immune system, especially infants and the elderly. However, they can also cause a host of other problems including memory loss and lethargy.
While all indoor environments have some amount of mold spores, they usually do not affect most people. They can, however, irritate the skin, eyes, and nose of some people. Some people, particularly those with a suppressed immune system or chronic lung disease may experience difficulty breathing.
Mold spores can be cleaned using commercial mold cleaners or diluted bleach (1 cup of chlorine bleach to 5 gallons of water). Mold growth can also be prevented by controlling the amount of moisture in indoor spaces and keeping them dry, particularly high-moisture areas like bathrooms. Ensure that showers, laundry rooms, and kitchens are well ventilated to prevent condensation and excessive moisture in these areas. Indoors, keep surfaces dry and clean and inspect for signs of rot or leaks regularly.